The manufacturing industry has always been defined by precision, timing and scale.
But in 2025, it’s being defined by something else entirely: unpredictability. Demand patterns are harder to forecast. Supply chains feel more fragile. And the pressure to deliver faster, cheaper and with less waste has never been higher.
In this environment, the manufacturers that thrive are not the ones with the largest factories or deepest inventories. They’re the ones who can adapt fast.
Agility in manufacturing isn’t a buzzword anymore. It’s the baseline. And to be agile, manufacturers need more than intuition. They need intelligent systems that help them see what’s coming, respond in real time and allocate resources with confidence.
This is where operational planning steps into the spotlight, particularly in the realms of inventory management and warehouse management.
Efficient inventory and warehouse operations are no longer just backend processes. They are strategic levers for profitability, customer satisfaction and resilience.
What Do We Mean by Inventory and Warehouse Management?
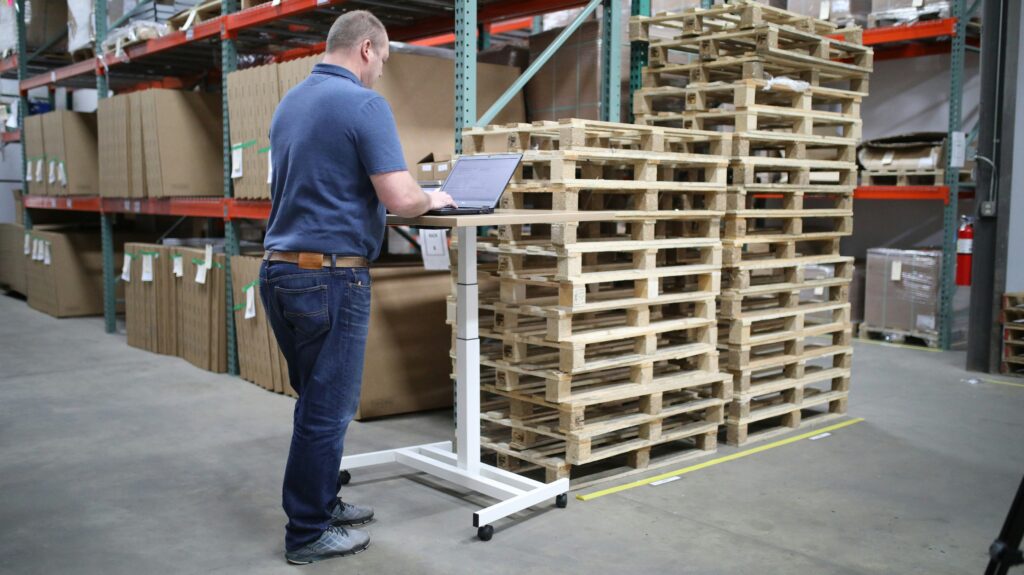
Inventory management refers to the way manufacturers track and manage stock levels, orders, raw materials, finished goods and deliveries. It ensures there’s enough on hand to meet demand but not so much that it ties up capital or clogs storage. The goal is balance — optimising for both availability and efficiency.
Warehouse management, on the other hand, focuses on how goods are stored, handled and moved within a warehouse or distribution centre. It’s about space, systems and speed — getting the right product to the right place at the right time, while reducing bottlenecks and manual errors.
Though closely linked, the two are not interchangeable. And understanding their differences is key to unlocking better operational performance.
Inventory vs Warehouse Management: What Sets Them Apart?
While both deal with physical goods, the scope of inventory management is broader. It spans the entire supply chain and touches forecasting, procurement, production and fulfilment.
In contrast, warehouse management is more location-specific, zooming into the logistics of how goods are stored and moved in a given space.
The technologies also vary.
Inventory systems often connect with ERP, forecasting and procurement tools. Warehouse systems may include robotics, barcode scanners and location tracking. The KPIs differ too. Inventory managers focus on stock turnover, carrying costs and stockouts. Warehouse teams track picking speed, order accuracy and space utilisation.
Together, they make up a critical part of inventory planning for manufacturers, and getting both right is foundational to operational success.
Why It’s Getting Harder to Keep Up
In theory, it sounds manageable. In practice, manufacturers are facing mounting pressure. Supply chains are more volatile. A delay in one part of the world ripples across global operations. At the same time, customers want faster delivery, more customisation and real-time visibility into their orders.
Traditional planning cycles (quarterly meetings, static spreadsheets, best-guess forecasts) simply can’t keep pace. Manufacturers need to know how much stock is in transit, which warehouse has available space and how changing demand will affect next month’s production. This is where many teams hit a wall.
The issue isn’t a lack of data. It’s a lack of connected, usable, real-time insights. And this is exactly where operational planning in manufacturing comes in.
What Is Operational Planning in Manufacturing?
Operational planning is the process of aligning day-to-day manufacturing activities with broader business objectives. It goes beyond annual forecasts or static budgets. Instead, it brings together real-time data, scenario planning and cross-functional collaboration to make smarter, faster decisions.
This includes everything from production scheduling to inventory management, warehouse flows, staffing and resource allocation. Unlike traditional planning, operational planning is continuous. It flexes with new information, supports proactive decision-making and helps teams pivot with confidence.
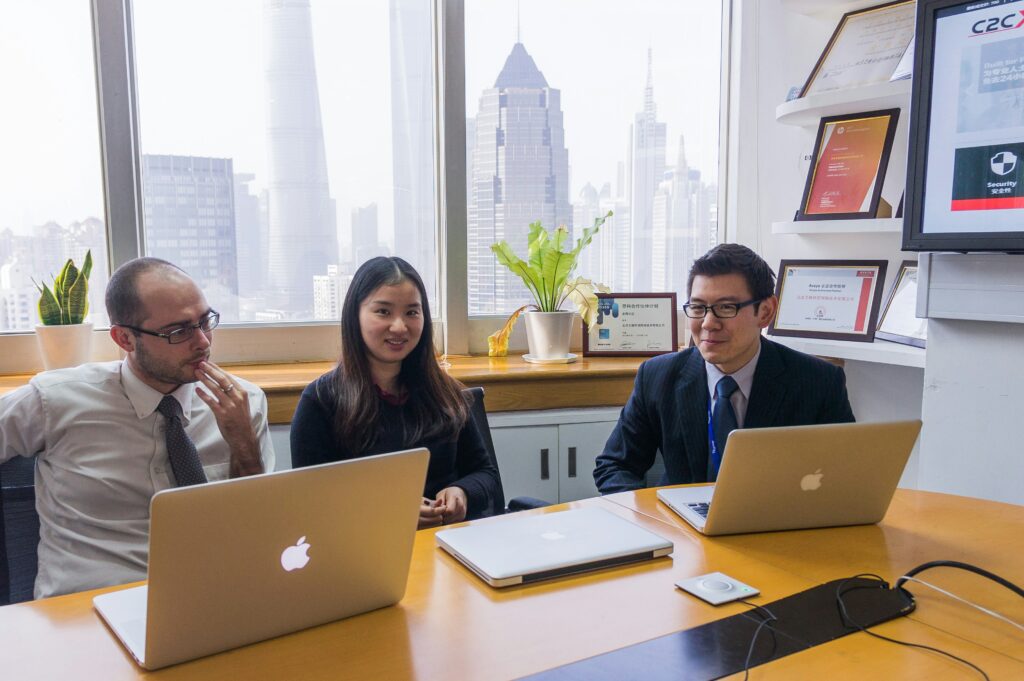
Why Workday Adaptive Planning Makes It All Work
A smart strategy needs a smart system to support it. Workday Adaptive Planning is a cloud-based platform that helps manufacturers shift from reactive to strategic. It brings together data from multiple systems, enabling teams to model scenarios, analyse performance and make course corrections in real time.
With Workday Adaptive Planning, manufacturers can:
- Forecast inventory levels across multiple sites
- Model different production and fulfilment scenarios
- Align operational plans with financial goals
- Collaborate across finance, operations and supply chain without version control headaches
The result? Less guesswork, more visibility and better decisions made faster.
Key Benefits for Manufacturers
When manufacturers adopt operational planning with the right technology, the payoff is real and measurable.
- Enhanced agility and responsiveness – Manufacturers can quickly respond to supply disruptions, demand spikes or capacity issues without overcorrecting.
- Improved resource utilisation and cost control – By planning more accurately, teams can reduce excess stock, minimise wastage and better manage labour and production time.
- Better alignment between operations and strategy – Instead of operating in silos, manufacturing teams can tie their plans to financial goals and company priorities.
- Empowered teams with self-service analytics – No more waiting on reports. Operations leaders can explore data on their own and take action quickly.
How to Get Started
Transitioning to smarter operational planning doesn’t have to be disruptive. The key is to start with clear priorities and the right tools. Begin by mapping out where the gaps are — whether it’s inventory visibility, warehouse coordination or forecasting accuracy.
Then, look at how Workday Adaptive Planning can connect those dots.
The platform integrates with existing systems and scales with your operations, making it a practical starting point for any size manufacturer. Whether you’re running lean or scaling up, this is about planning smarter, not harder.
Final Thoughts
The future of manufacturing won’t be shaped by those who wait for certainty. It will be shaped by those who can plan, adapt and act all at once.
Inventory management, warehouse management and operational planning in manufacturing are no longer separate threads. They’re part of a larger fabric of responsiveness and resilience.
With a platform like Workday Adaptive Planning, manufacturers don’t just keep up, they stay ahead. It’s time to explore what’s possible when planning becomes a strategic advantage.
Want to see it in action? Reach out to schedule a demo or learn more about how leading manufacturers are transforming their operations.
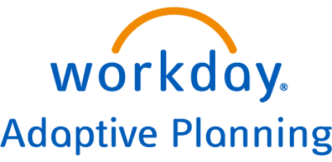